
- Airfoil audio speed up slow down update#
- Airfoil audio speed up slow down software#
- Airfoil audio speed up slow down code#
- Airfoil audio speed up slow down Pc#
In particular, UAV propeller design will benefit from improved performance data where a highly coupled relationship exists between aircraft drag, engine characteristics, and propeller performance.
Airfoil audio speed up slow down code#
The latter is especially true for slower speed conditions where applicability of the TAIR code may be uncertain. These data are most useful when utilized on a comparative basis to identify the effects of design changes when test data exist to anchor performance of particular design.
Airfoil audio speed up slow down update#
Over one week of continuous processing on a high-end workstation is required to update the performance data files. A batch processing system is used to update these data when improvements are made to any of the elements within the performance software. The performance data are all computer generated using the theoretical and computational methods described above. These performance data provide estimates of thrust, torque and efficiency over a broad range of model speeds and engine RPM.
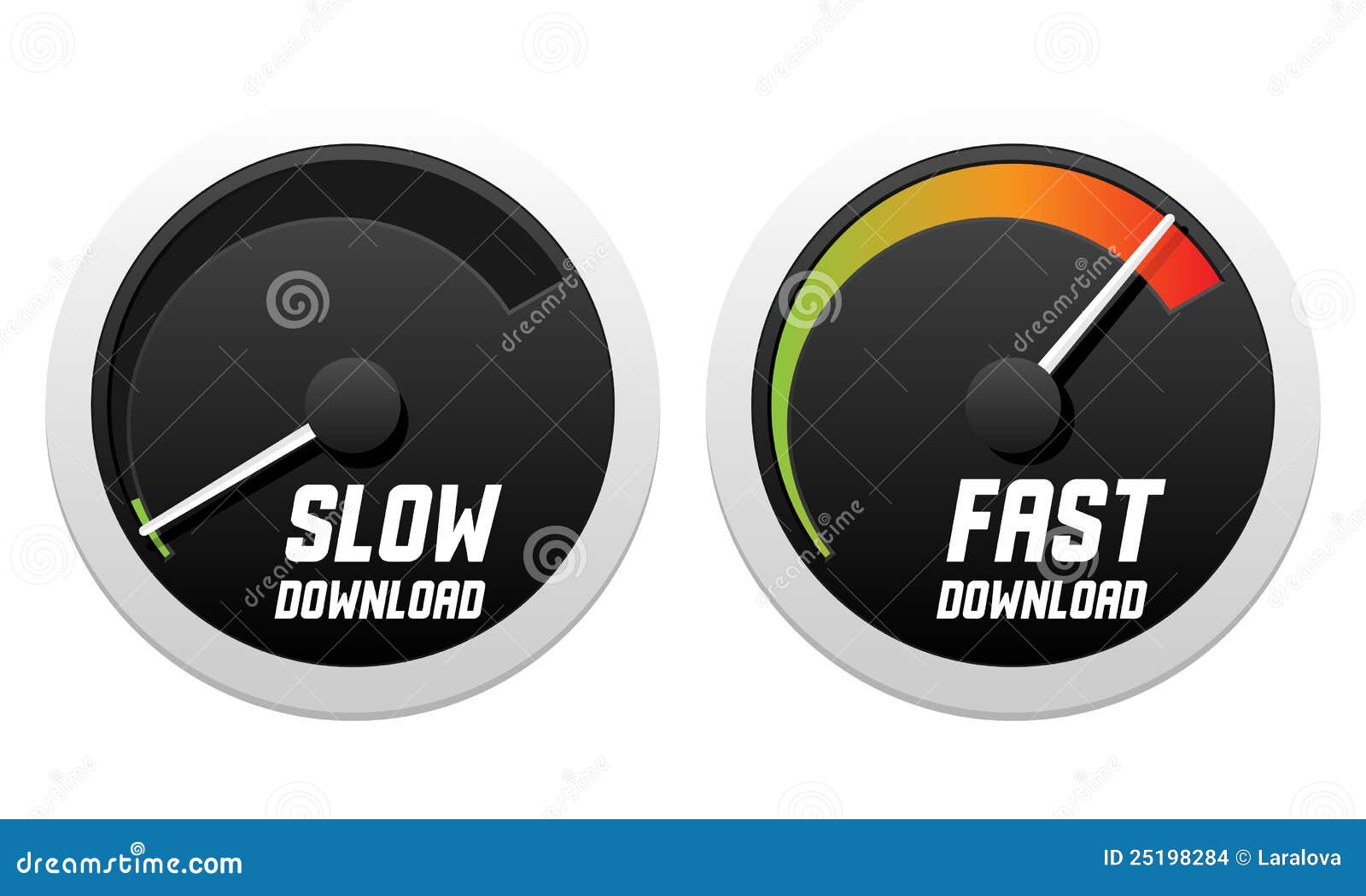
Performance Data FilesĪPC provides Performance Data files for all propellers currently in production. We expect that this improvement will substantially increase predictive accuracy of performance data at low Reynolds numbers. Stability is an essential property for batch processing described below.ĪPC is currently developing the ability to analyze airfoils at slower speed conditions within our design software. This code has been heavily developed to provide very stable (numerical) performance over a broad range of environments. The TAIR code is most appropriate for high speed conditions. Empirical data are used to characterize minimum drag levels under low propeller loading conditions. Lift-drag data are computed using the NASA TAIR code, using representative airspeed and engine RPM to set Mach number distributions. These flow field effects are computed using 3D potential flow theory. For some applications, (i.e., an AT-6), the fuselage shape and/or cowling can significantly affect the airflow through the propeller. Vortex theory is the basis for the computational method used to calculate blade loading. Hub geometry for 3 and 4 bladed propellers is very complex because of the need to match mold parting lines at all points on the mold surface perimeter. The aerodynamic-dominant airfoil must smoothly transition into a structural-dominant shape in a manner that emphasizes strength consistent with milling machine tool constraints. Hub GeometryĬross-section geometry in and near the hub region is defined with specialized algorithms. Thin electric, slow-fly, and multi-rotor propellers typically blend the low Reynolds number Eppler E63 airfoil (inboard) with a Clark-Y similar airfoil near the tip. For applications where Mach number effects become significant near the tip, either pitch washout or camber reduction are used to minimize Mach drag rise. Most blades have some washout near the tip. This alters the zero-lift angle by approximately one degree and provides greater lift without having to twist the blade more. Also, the aft region is somewhat thicker. The dominant basis for the primary airfoil shape used in most APC propellers is similar to the NACA 4412 and Clark-Y airfoils, except the leading edge is somewhat lower. Capability exists to smoothly “splice” together widely different airfoil shapes. The airfoils may have arbitrary shapes defined with either tabular data (splined cubic fits) or analytical functions typically used for NACA airfoils. The parting line must be very precise and continuous around the entire perimeter of the mold cavity to allow precision molding of the very thin airfoils used on many of the APC propellers.
Airfoil audio speed up slow down software#
The design of the computer software used to define airfoils, and the resulting CNC motion, dominantly reflects parting line driven requirements. CNC milling machines are used to create the molds. Injection Molding Parting Line RequirementsĪPC propellers are injection molded using a pair of mold halves. This system has been undergoing continuous development and improvement for over two decades.
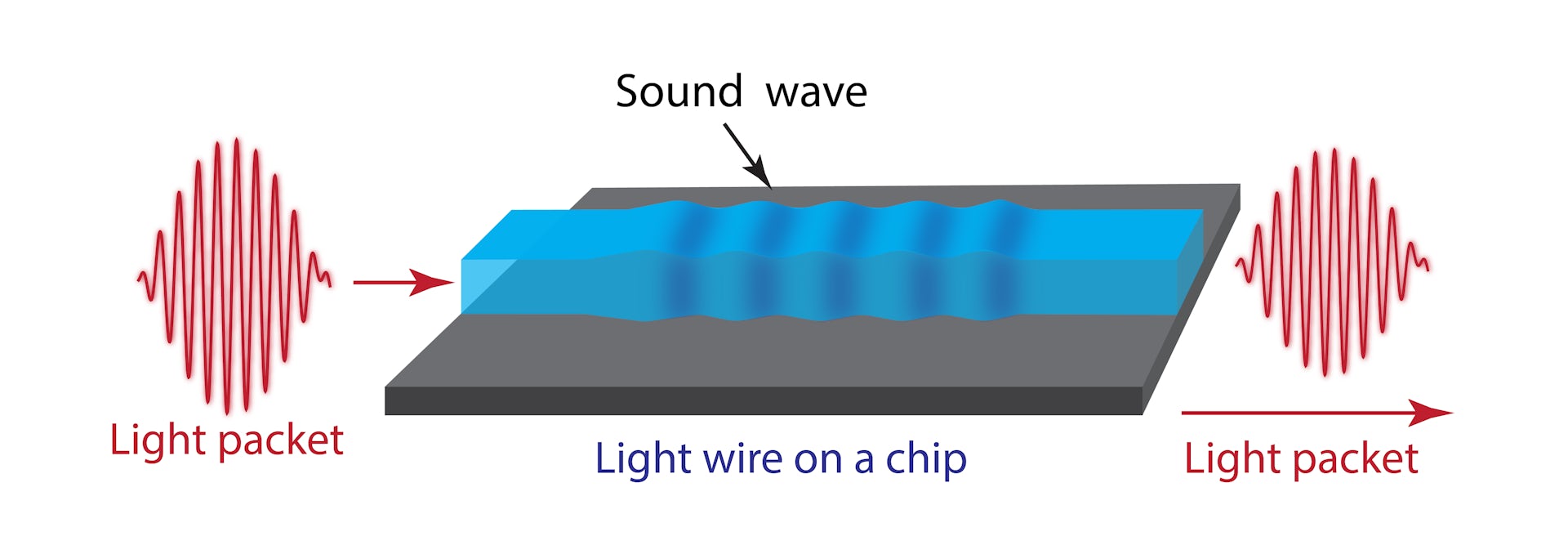
The software is specifically tailored for model and UAV propeller design and manufacture.
Airfoil audio speed up slow down Pc#
Engineering Design Process Used to Develop APC PropellersĪPC propeller development uses a proprietary PC based CAD-CAM system.
